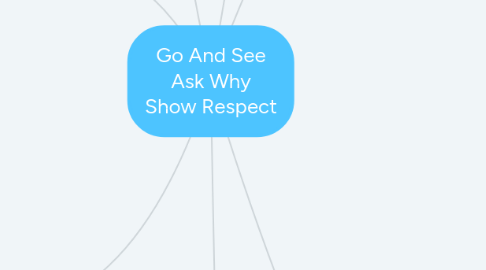
1. Not MBWA
1.1. Management By Walking Around
1.2. Focus on Leader being Visible
1.3. Aims to build relationships
1.4. Lacks clear purpose
2. Take Action
2.1. "Just Do It"
2.2. PDCA
2.3. Kaizen
3. Gemba "Actual Place"
3.1. Where the Work Happens
3.2. When it's happening
3.3. While People are Working
4. Class Exercises
4.1. Week 6
4.1.1. Discover value of "Go and See"
4.1.1.1. Go to Campus
4.1.2. Discover value of "Purpose"
4.1.2.1. Wear Different Hats
4.1.3. Learn to identify Value vs Non-Value Add
4.1.3.1. Identify the VA in different places
4.2. Week 7
4.2.1. Expand Awareness to include Muri, Mura, and Muda
4.2.1.1. Open Discussion
4.2.1.2. Student Experience
4.2.1.3. Expanded Walk with Purpose
5. Prepared by: Brett Nelson, P.Eng. For Conestoga College Quality Assurance & Manufacturing Management 13-Feb-2023
6. Purpose
6.1. KPI's & Standards
6.1.1. Quality
6.1.1.1. Yield
6.1.1.2. GRR
6.1.1.3. QMS Compliance
6.1.2. Cost
6.1.2.1. Equipment Utilization
6.1.2.2. Employee Utilization
6.1.2.3. Tooling vs Budget
6.1.3. Delivery
6.1.3.1. Cycle and Set-Up Time vs Standards
6.1.3.2. Material Waiting Time
6.1.4. Motivation & Employee Well-Being
6.1.4.1. Confidence
6.1.4.2. Ownership
6.1.4.3. Satisfaction
6.1.4.4. Health & Safety
6.2. Mura (Imposed Uneveness/imbalance) (斑)
6.3. Muri (Impossible/Unreasonableness) (無理)
6.4. Muda (Waste) (無駄)
6.4.1. Defects
6.4.2. Overproduction
6.4.3. Waiting
6.4.4. Non-Utilized Resources
6.4.5. Transport (Product)
6.4.6. Inventory
6.4.7. Motion (People or Machine)
6.4.8. Effort
6.4.9. Energy
6.4.10. Space
7. Plan
7.1. Not just "get out there and be seen"
7.2. See the Truth
7.3. Hear the Truth
7.3.1. Employee Feedback / Opinion
7.4. Fix or Improve Real Issues
7.4.1. Have a positive impact - help your team!
7.5. Investigate Concerns
7.5.1. Customer Complaints
7.5.2. KPI Dashboards
7.5.3. Audit Results
7.6. Consider "randomizing" where, what, and when to remove bias and expand coverage
8. People
8.1. Develop own Understanding - observe and ask questions
8.2. Seek Ideas, Feedback
8.3. Training / Engagement / Awareness
8.3.1. Explain Targets
8.3.2. Share Vision
8.3.3. Teach / Mentor
8.3.4. Empower Teams
8.4. Celebrate Success
8.4.1. Celebrate Small Wins
8.4.2. Recognize Effort
8.4.3. Encourage Continuous Improvement
9. Observe, Engage and Ask Questions
9.1. Mura (Uneveness)
9.1.1. Alternating High-Low (Rush-Wait) Demand
9.1.2. Bottlenecks
9.1.2.1. Product accumulating ahead of a workstation/process step
9.1.3. Interrupted Flow
9.1.3.1. Hesitation
9.1.3.2. Not Confident
9.1.3.3. Struggling with task
9.1.4. Variation
9.1.4.1. Person does same way each time (repeatability)
9.1.4.2. All people do as each others (reproduceability)
9.1.4.3. Different Machine/Equipment being used
9.1.4.4. Different Tooling being used
9.1.4.5. Variations in Material / Supplier Quality
9.1.5. Push (Not Pull)
9.1.5.1. Not demand-driven work
9.2. Muri (Overburden, Unreasonableness)
9.2.1. Impossible Task
9.2.2. Impossible Deadline
9.2.3. Inferior Tooling or Equipment
9.2.3.1. Limited Capacity
9.2.3.2. Poor Capability (low Cmk)
9.2.3.3. Worn / Old / Poor Repair / Low Technology
9.2.4. Insufficient Training
9.2.4.1. Operator Not trained
9.2.4.2. Insufficient, Unclear, or Wrong Instructions
9.2.5. Over-work (extended shifts, forced overtime)
9.2.6. Fatigue / Poor Ergonomics
9.3. Muda
9.3.1. Waste = Any Non-Value Add Activity Focus on the Product, but also watch the People!
9.3.1.1. Any poor quality or risk to quality
9.3.1.1.1. Check incoming material quality
9.3.1.1.2. Check understanding of drawing / GD&T requirements
9.3.1.1.3. Check Gages for Calibration
9.3.1.1.4. Check operator use of gages
9.3.1.1.5. Check machine capability
9.3.1.1.6. Check Machine Maintenance
9.3.1.1.7. Check Inspection Record for Out of Tolerance or Close to Limits
9.3.1.1.8. Rework
9.3.1.2. Product Not in Motion
9.3.1.2.1. Waiting for something / someone
9.3.1.2.2. Operator Looking / Searching for something
9.3.1.3. Product Being Worked On
9.3.1.3.1. Effort/Motion that isn't adding value
9.3.1.3.2. Overwork
9.3.1.3.3. Rework
9.4. Value Add
9.4.1. Effort that Adds Value to Product for Customer
9.4.2. Completing a Required Operation
9.4.2.1. Should be a planned step
9.4.2.2. Should be in planned sequence
9.4.2.3. Taking only the Planned Amount of Time
10. Lean Leadership
10.1. Focus on Team
10.1.1. Their performance
10.1.2. Their job satisfaction
10.2. Enablers - Motivation & Ability
10.2.1. Personal
10.2.2. Social
10.2.3. Structural
11. W5 - Go And See "Genchi Genbutsu" (現地現物
11.1. Why?
11.1.1. To Learn the Truth
11.1.1.1. "Genjitsu" (現実) - Reality
11.1.2. To Support your Team
11.2. How?
11.2.1. Ask Why
11.2.2. Go To Gemba gen (現 = actual) ba (場 = place)
11.2.2.1. Wear all your "Hats" (Responsibilities) - focus on 1 each walk, random/rotation
11.2.2.1.1. Quality
11.2.2.1.2. Cost - Resource Usage
11.2.2.1.3. Delivery
11.2.2.1.4. Safety
11.2.2.1.5. Training
11.2.2.1.6. Procedures
11.2.3. Show Respect
11.3. What?
11.3.1. Look for Waste
11.3.2. Look for Risk
11.3.3. Look for Opportunity
11.3.3.1. Should See
11.3.3.2. Might See
11.3.3.3. Did See
11.3.4. "A leaders hould be able to see things that other people are not able to see" Sadhguru
12. W6 - Finding Opportunities to Improve
12.1. KPI Metrics
12.2. Muri
12.3. Mura
12.4. Muda
12.5. Anything that doesn't look right!
12.5.1. Someone is having a hard time with something
12.5.2. Someone keeps double-checking their work
12.5.3. Someone is searching for something
12.5.4. Someone is waiting for something/someone