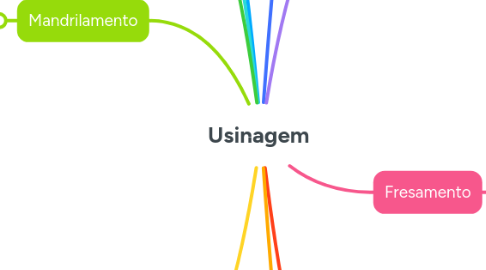
1. Avarias e Desgaste da Ferramenta de Corte
1.1. Desgaste de flanco
1.1.1. ocorre na **superfície de folga da ferramenta**
1.1.2. causado pelo contato entre a
1.1.2.1. ferramenta
1.1.2.2. peça
1.2. Lascamento
1.2.1. partículas maiores
1.2.1.1. retiradas de uma só vez
1.2.2. prejudica o acabamento superficial da peça
1.2.3. se continuar crescendo
1.2.3.1. provoca a quebra da ferramenta
1.2.4. ocorrência
1.2.4.1. ferramentas fabricadas com **material frágil**
1.2.4.1.1. baixa capacidade de deformação
1.2.4.2. aresta de corte
1.2.4.2.1. pouco reforçada
1.3. Desgaste de cratera
1.3.1. **superfície de saída da ferramenta**
1.3.2. causado pelo atrito entre
1.3.2.1. ferramenta
1.3.2.2. cavaco
1.4. Trincas térmicas
1.4.1. fluido refrigerante
1.4.1.1. agrava o problema
1.4.1.1.1. mudança rápida de temperatura
1.5. Deformação plástica da aresta de corte
1.5.1. pode ocorrer devido às altas
1.5.1.1. temperaturas
1.5.1.2. e pressões
1.5.1.2.1. na região de corte
1.5.2. provoca
1.5.2.1. deficiências do controle de cavacos
1.5.2.2. deterioração do acabamento superficial da peça
1.5.3. crescimento dessa deformação
1.5.3.1. gera a quebra da aresta de corte da ferramenta de usinagem
1.6. Para reduzir o desgaste
1.6.1. diminuir
1.6.1.1. a rotação da máquina
1.6.1.2. o avanço
1.6.2. empregar fluido de arrefecimento
1.7. Equação de Taylor
1.7.1. T = (C/Vc)^(1/y)
1.7.1.1. T
1.7.1.1.1. tempo de vida da ferramenta em minutos
1.7.1.2. C e y
1.7.1.2.1. parâmetros para a vida da ferramenta
2. Ferramentas de Corte
2.1. Geometria da cunha cortante
2.1.1. características das bordas de corte da ferramenta de usinagem
2.1.1.1. ângulos de inclinação
2.1.1.2. raios
2.1.1.3. ângulos de saída
2.1.2. papel crítico na
2.1.2.1. determinação da qualidade da usinagem
2.1.2.2. força de corte
2.1.2.3. eficiência do processo
2.2. Forças e potências de corte
2.2.1. fundamental para
2.2.1.1. projeto de ferramentas de corte
2.2.1.2. determinar quanto tempo uma ferramenta pode ser usada
2.2.1.2.1. antes de necessitar de substituição
2.2.1.3. evitar falhas prematuras das ferramentas
2.2.1.4. otimizar o processo de usinagem
2.3. **Materiais** utilizados
2.3.1. para fabricar ferramentas de corte
2.3.2. devem ser escolhidos
2.3.2.1. com base na sua capacidade de resistir
2.3.2.1.1. ao desgaste
2.3.2.1.2. à deformação
2.4. Fluidos de corte
2.4.1. exemplo
2.4.1.1. óleos de corte
2.4.2. usados durante a usinagem para
2.4.2.1. resfriar a ferramenta e a peça
2.4.2.2. reduzir o atrito
2.4.2.3. remover cavacos
2.4.2.4. melhorar a qualidade do acabamento da superfície usinada
2.4.3. papel importante na
2.4.3.1. preservação da vida útil da ferramenta
2.4.3.2. eficiência do processo de usinagem
2.5. Condição econômica
2.5.1. aspecto fundamental a ser considerado na usinagem
2.5.1.1. escolha
2.5.1.1.1. das ferramentas de corte
2.5.1.1.2. dos parâmetros de corte
2.5.1.1.3. dos materiais de ferramentas
2.5.1.1.4. dos métodos de usinagem
2.5.1.2. eficiência da usinagem
2.5.1.2.1. minimizar desperdícios de
3. Outros Processos
3.1. Furação
3.1.1. Criação de furos em uma peça de metal usando uma broca
3.2. Jateamento
3.2.1. Jatos de partículas abrasivas para
3.2.1.1. remover material
3.2.1.2. criar texturas em uma superfície
3.3. Aplainamento
3.3.1. ferramenta cortante se desloca
3.3.1.1. em linha reta
3.3.1.2. sobre a superfície da peça
3.3.2. remoção de uma fina camada de material
3.3.2.1. superfície plana
3.3.2.2. acabamento uniforme
3.4. Roscamento
3.4.1. criação de roscas em peças metálicas
3.4.2. macho de rosca
3.4.2.1. corta as ranhuras na superfície da peça
3.4.2.1.1. cria a rosca
3.5. Retificação
3.5.1. processo de usinagem por abração
3.5.1.1. remoção de material
3.5.1.1.1. realizada através de uma operação de esmerilhamento
3.5.2. utilizado para
3.5.2.1. obter superfícies
3.5.2.1.1. extremamente
3.5.2.1.2. com formas complexas
3.5.2.2. proporcionar acabamento de alta qualidade
3.6. **Eletroerosão**
3.6.1. promove a remoção do metal
3.6.1.1. por meio de uma série discreta de descargas elétricas
3.6.1.1.1. faíscas
3.6.1.1.2. provocam temperaturas localizadas
3.6.2. processo não convencional de usinagem
4. Mandrilamento
4.1. Usinagem de um diâmetro interno de um orifício preexistente
4.2. Obtenção de superfícies de revolução
4.2.1. com auxílio de ferramentas de barra
4.3. Ferramenta gira
4.4. Peça
4.4.1. ou ferramenta
4.4.2. se desloca simultaneamente
4.4.2.1. segundo uma trajetória determinada
5. Brunimento
5.1. Utilizado para
5.1.1. melhorar a qualidade superficial das peças
5.1.2. criar superfícies internas ou externas com alta
5.1.2.1. precisão
5.1.2.2. planicidade
5.1.2.3. acabamento
5.1.3. aplicações em que a
5.1.3.1. precisão dimensional
5.1.3.2. e qualidade da superfície
5.1.3.2.1. são críticas
5.2. Eficaz na obtenção de superfícies
5.2.1. planas
5.2.2. lisas
6. Introdução
6.1. Processo mecânico
6.1.1. confere à peça
6.1.1.1. forma
6.1.1.1.1. através da **remoção de material sob a forma de cavaco**
6.1.1.2. dimensões
6.1.1.3. ou acabamento superficial
6.2. Comumente divididos entre
6.2.1. usinagem convencional
6.2.2. processos abrasivos
6.2.3. processos não tradicionais
7. Torneamento
7.1. Ferramenta monocortante
7.1.1. movimento de avanço
7.1.1.1. por translação
7.1.1.2. sobre a peça
7.1.1.2.1. com movimento rotativo
7.2. Velocidade de corte
7.2.1. Vc = π*d*n/1000
7.2.1.1. Vc
7.2.1.1.1. m/min
7.2.1.2. d
7.2.1.2.1. mm
7.2.1.3. n
7.2.1.3.1. rpm
8. Fresamento
8.1. Corte de um material
8.1.1. utilizando uma ferramenta rotativa
8.1.1.1. múltiplas arestas cortantes
8.1.1.2. fresa
8.2. Fresa
8.2.1. fixada em um eixo rotativo
8.2.2. movida
8.2.2.1. em relação à peça de trabalho
8.2.2.2. para cortar o material
8.2.3. gira e translada
8.3. Peça
8.3.1. fixada na mesa
9. Serramento
9.1. Processo de corte
9.2. Lâmina de serra é usada para remover material de uma peça
9.3. Fenda estreita
9.3.1. retirada de uma peça
9.3.1.1. por uma ferramenta
9.3.1.1.1. composta de uma série de dentes com espaçamentos estreitos
10. Brochamento
10.1. Remoção de material
10.1.1. usando uma ferramenta especializada
10.1.1.1. brocha
10.1.1.1.1. desloca-se de forma retilínea
10.1.1.1.2. utilizada para realizar cortes progressivos em uma peça
10.1.1.1.3. multicortante
10.2. Eficaz para criar
10.2.1. perfis complexos
10.2.2. formas internas precisas