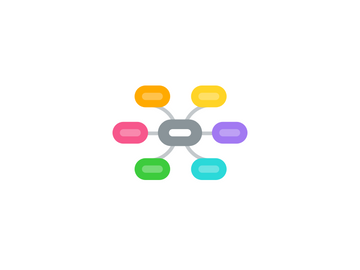
1. Wat zijn de waarde toevoegende stappen?
1.1. THEORY OF CONSTRAINTS
1.1.1. Kies wat je wilt optimaliseren
1.1.2. Optimaliseer capaciteit bij bottleneck
1.1.3. Pas de org. aan bij de bottleneck
1.1.4. Verbeter de bottleneck
1.1.5. Begin opnieuw
1.2. VALUE ADD ANALYSIS
1.2.1. CVA
1.2.1.1. Verbeteren
1.2.2. BVA
1.2.2.1. Reduceren
1.2.3. NVA
1.2.3.1. Elimineren
1.3. WASTE
1.3.1. Transport
1.3.2. Inventory
1.3.3. Motion
1.3.4. Waiting
1.3.5. Over-production
1.3.6. Over-processing
1.3.7. Defects
1.3.8. Skills
1.4. Go to the Gemba!
2. Streef naar Perfectie
2.1. 5S
2.1.1. Scheiden
2.1.2. Schikken
2.1.3. Schoonmaken
2.1.4. Standaardiseren
2.1.5. Stimuleren en in stand houden
2.2. VISUAL MANAGEMENT
2.2.1. Visueel maken van gewenst gedrag
2.3. POKA YOKE
2.3.1. Zorgdragen dat processen niet meer fout kunnen gaan
2.3.2. Hoe eerder fouten worden ontdekt, hoe beter
2.3.2.1. Defecten
2.3.2.1.1. Gebreken waardoor product niet compleet is
2.3.2.2. Fouten
2.3.2.2.1. Verkeerde actie of handeling
2.4. 5 TIMES ?
2.4.1. Om root cause te achterhalen
2.5. SPAGHETTIDIAGRAM
2.5.1. Visueel maken van beweging
2.6. STANDUP'S
2.6.1. dagelijks met eigen medewerkers
2.7. KAIZEN
2.7.1. Projecten die 3-5 dagen duren
3. Produceer de juiste hoeveelheid van de juiste artikelen/diensten op het juiste moment zodat het voldoet aan wat de klant wil. Elimineren van verspilling (minimale kosten, juiste Q, minimale tijd)
4. Breng waardestroom in kaart
4.1. VALUE STREAM MAPPING
4.1.1. Datarijk procesmap
4.1.2. Proces- materiaal en informatiestromen
4.1.2.1. Bepaal proces om in kaart te brengen
4.1.2.2. Teken de proces-stroommap
4.1.2.3. Voeg materialen en data verzamelboxen toe
4.1.2.4. Voeg procestijd en doorlooptijd toe
4.1.3. Huidige situatie vastleggen
4.1.4. Breng waardestijging in kaart
4.1.4.1. CVA, BVA en NVA
5. Creëer FLOW
5.1. PROCESSFLOW
5.1.1. Reduceren van overdracht
5.1.2. Kleine batches one-piece-flow
5.1.3. Multi-skilled personeel
5.1.4. Lage voorraden
5.1.5. Lage omsteltijden SMED
5.1.6. Produceren volgens Takt Time
5.2. TAKT TIME
5.2.1. Het tempo waarin producten moeten worden gemaakt om te voldoen aan de klantvraag. NB: Onafhankelijk van aantal medewerkers!
5.2.2. Effectief beschikbare tijd / Klantvraag
5.3. PROCESS CYCLE TIME
5.3.1. De standaard tijd in welke ieder proces of processtap een deel van het product produceert. Ligt zo dicht mogelijk tegen maar wel onder de Takt time.
5.4. EXIT RATE
5.4.1. Aantal eenheden wat max gemaakt kan worden in de beschikbare tijd
5.5. PROCESS LEAD TIME PLT
5.5.1. WIP / Exit Rate
5.6. PROCESS CYCLE EFFICIENCY PCE
5.6.1. CVA in tijd / PLT * 100%
6. Van Push naar Pull
6.1. PULL
6.1.1. De klantvraag of trigger in volgende processtap, bepaald het productieritme
6.1.1.1. Exit initieert start
6.1.2. Verlagen van voorraad, voorkomen van WIP, geen achterstallige opdrachten, robuuster proces, grotere learning cycle
6.2. WIP CAP
6.2.1. Maximale hoeveelheid onderhanden werk binnen een proces
6.2.2. Berekeningswijze
6.2.2.1. Bepaal de Target PCE
6.2.2.2. Bereken de target PLT
6.2.2.3. Bereken de WIP CAP
6.3. TARGET PLT
6.3.1. WIP CAP / Exit Rate (in tijd!!)